La corrosión juega un papel muy importante en la industria de la construcción, la industria naval y la industria petrolera, debido a que las estructuras metálicas son elementos fundamentales que son utilizados en una amplia gama de aplicaciones debido a su resistencia y durabilidad.
Estas estructuras que en su mayoria son de acero al carbón, acero inoxidable y aluminio, están expuestas a condiciones ambientales adversas que pueden comprometer su integridad, para prevenir esto la industria ha desarrollado sistemas de protección pasivos y activos contra la oxidación y la corrosión, ayudando asi a proteger estos activos y el personal que trabaja en ellos.
¿QUÉ ES LA CORROSIÓN DEL ACERO?
Es el deterioro que experimenta este material al ser expuesto a sustancias corrosivas, sucede cuando hay una diferencia de potencial entre dos puntos y se establece una corriente de electrones, un material cede electrones que migran hacia otro material, convirtiéndolo en un ánodo y causa de la oxidación. Quien recibe los electrones se convierte en un cátodo y experimenta la reducción.
El acero se corrode debido a su naturaleza inestable, ya que el hierro (Fe), que es uno de sus componentes principales tiende a regresar a su estado natural de óxido de hierro, debido a las diferencias químicas entre las piezas involucradas.
Las reacciones electroquímicas se pueden representar mediante la siguiente ecuación
Fe + 3O 2 + 2H 2 O = 2Fe 2 O 3 H 2 O
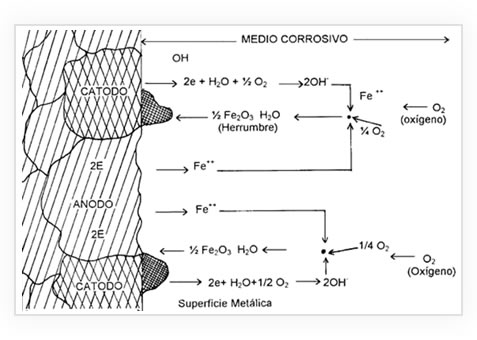
Imagen extraida de https://www.lamigal.com/metal-acero-corrosion/corrosion-del-acero.html
El proceso de corrosión requiere la presencia simultánea de agua y oxígeno, en ausencia de cualquiera de ellos, no se produce, ocurre en la superficie del metal en contacto con un electrolito se presentan uno o más de los siguientes factores:
- Alta humedad, es decir, una humedad superior al 60%.
- Contaminación atmosférica, que aporta impurezas como sulfuros (se originan a partir del gas de dióxido de azufre producido durante la combustión de combustibles fósiles) y cloruros (en escencia son sales).
- La presencia de cascarilla de laminación con grietas o discontinuidades que actúa como el polo positivo (cátodo) mientras que el acero actúa como el polo negativo (ánodo).
¿QUÉ DIFERENCIA HAY ENTRE OXIDACIÓN Y CORROSIÓN?
La oxidación es un proceso superficial en el cual el metal reacciona con el oxígeno del ambiente, formando una capa de óxido en su superficie. Esta capa se puede eliminar mediante técnicas de limpieza mecánica o el uso de productos químicos específicos.
Por otro lado, la corrosión es un proceso químico más complejo que implica la interacción entre el elemento, el oxígeno y otros agentes corrosivos, como la humedad o sustancias químicas agresivas, afecta a diversos materiales pero es más común en metales.
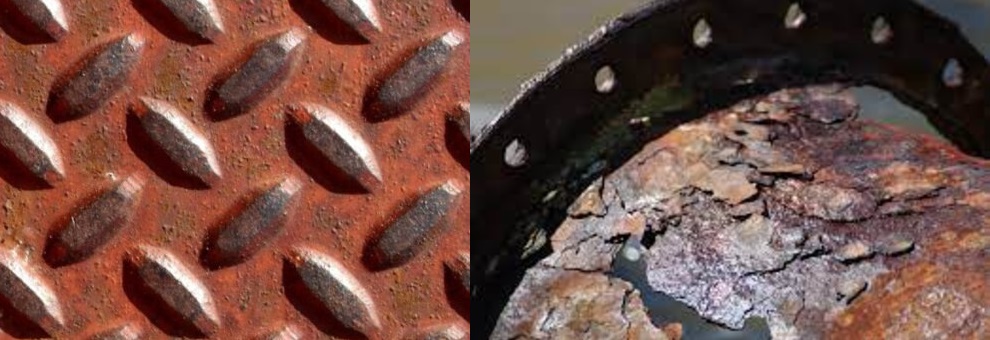
A diferencia de la oxidación, la corrosión penetra más profundamente en el material y puede causar un deterioro significativo, el metal corroído puede perder resistencia, debilitar la estructura e incluso desarrollar grietas y fracturas.
Una diferencia importante es la velocidad de desarrollo de cada proceso, la oxidación puede ocurrir gradualmente a lo largo del tiempo pero la corrosión puede progresar de forma mucho más rápida y agresiva, especialmente en ambientes propicios como zonas costeras o industrias químicas.
TIPOS DE CORROSIÓN.
Existen diferentes formas de clasificar los tipos de corrosión
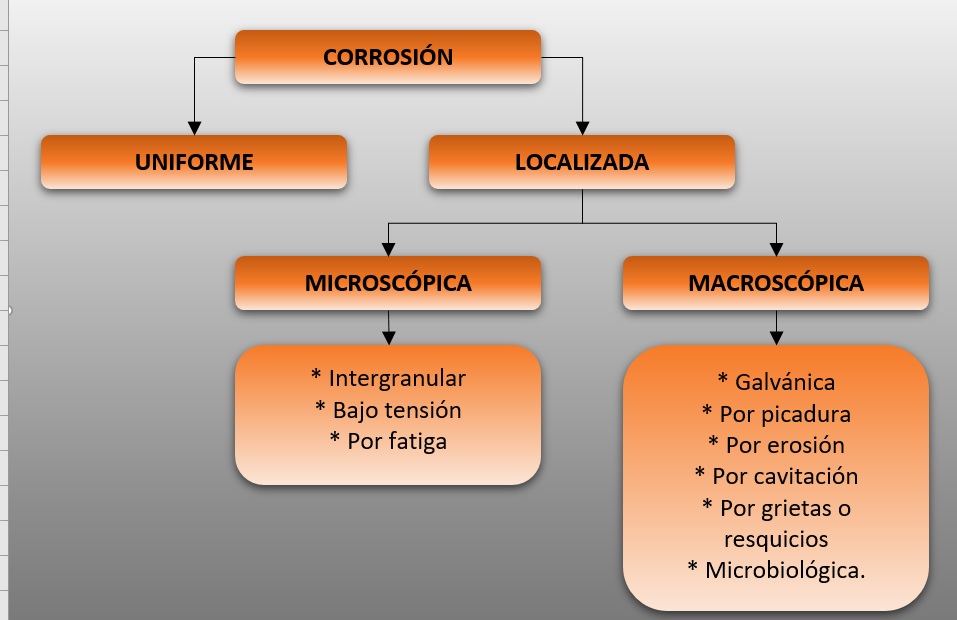
Uniforme.
Es la más común, también conocida como corrosión generalizada ocurre de manera homogénea sobre la superficie del material expuesto al ambiente corrosivo.
Intergranular.
Se produce a lo largo de los límites de grano del metal, generalmente debido a la sensibilización de ciertos aceros al ser expuestos a temperaturas elevadas.

Bajo tensión.
Aparece cuando se cumplen tres condiciones, un medio especifico, una tensión aplicada y un metal sencible a este tipo de corrosoion, se puede originar por un tensiones residuales en el proceso de conformado.
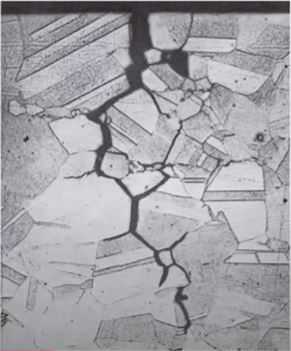
Por fatiga.
Debe haber una fuerza periodica que fatiga el elemento, es muy similar a la anterior.
Galvánica.
Es el resultado de la interacción entre dos metales diferentes en contacto eléctrico en presencia de un electrolito, lo que crea un flujo de corriente que acelera la corrosión del metal más susceptible.
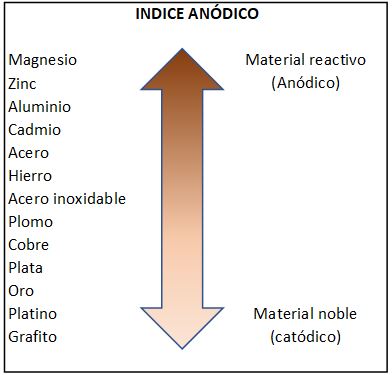
Por picadura o «pitting»
Se produce cuando pequeñas áreas de la superficie del metal sufren corrosión localizada, formando cavidades o «picaduras». Es común en metales como el aluminio y el acero inoxidable, en este tipo de corrosión se crean pequeños hoyos o agujeros en el metal. los orificios creados pueden ser tan pequeños que forman canales a través de los materiales debilitando su estructura.

Imagen extraida de https://www.lamigal.com/metal-acero-corrosion/corrosion-del-acero.html
Por erosión.
Los fluidos con o sin sólidos en suspensión causan deterioro al desplazarse por encima de un cierto valor umbral de velocidad sobre una superficie metálica. La velocidad del fluido influye en el grado de corrosión, ya que puede provocar el levantamiento de capas protectoras por erosión e incluso de material metálico.

Imagen extraida y adaptada de https://ingenieromarino.com/corrosion-y-tratamiento-de-superficies-tratamiento-de-la-obra-viva-del-buque/
Por cavitación.
Ocurre en sistemas donde hay un flujo de líquido a alta velocidad, como en bombas y hélices, causando la formación y colapso de burbujas que erosionan la superficie del metal. Se asemeja a picaduras por corrosión, pero en la cavitación, las zonas dañadas son más compactas y la superficie es más irregular. Se atribuye parcialmente a efectos de desgaste mecánico. La corrosión interviene cuando el colapso de la burbuja destruye la película protectora en los siguientes pasos:
- Una burbuja de cavitación se forma sobre la película protectora.
- El colapso de la burbuja causa la destrucción local de la película.
- La superficie no protegida del metal queda expuesta al medio corrosivo y se forma una nueva película mediante una reacción de corrosión.
- Se forma una nueva burbuja en el mismo lugar, debido al aumento del poder nucleante de la superficie irregular.
- El colapso de la nueva burbuja destruye nuevamente la película.
- La película se forma de nuevo y el proceso se repite indefinidamente hasta formar huecos bastante profundos.
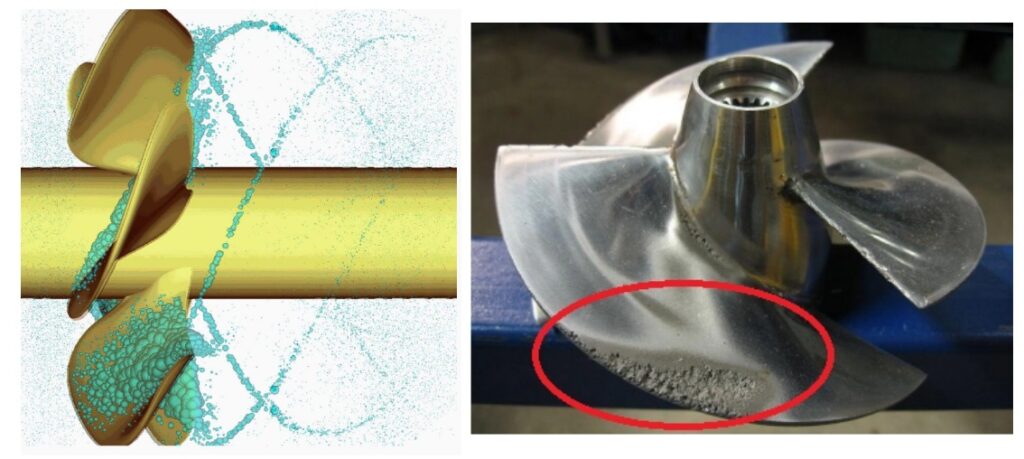
Imagen extraida y adaptada de https://ingenieromarino.com/corrosion-y-tratamiento-de-superficies-tratamiento-de-la-obra-viva-del-buque/
Corrosión por grietas o resquicios.
Las grietas pueden formarse debido a detalles de diseño o aplicación de soldadura. El proceso de corrosión utiliza rápidamente el oxígeno disponible en la grieta y la entrada a la hendidura se vuelve catódica, ya que puede satisfacer la reacción catódica que demanda oxígeno. En este punto, la punta de la hendidura se convierte en un ánodo localizado, lo que resulta en altas tasas de corrosión.
Microbiológica.
Es causada por microorganismos (bacterias, hongos o algas) que pueden iniciar, facilitar o acelerar el deterioro de un material metálico en un proceso electroquímico , comúnmente encontrado en ambientes marinos o en sistemas de agua, es conocida tambien como corrosión influida microbiológicamente o MIC (por sus siglas en inglés, Microbiologically Influenced Corrosion).
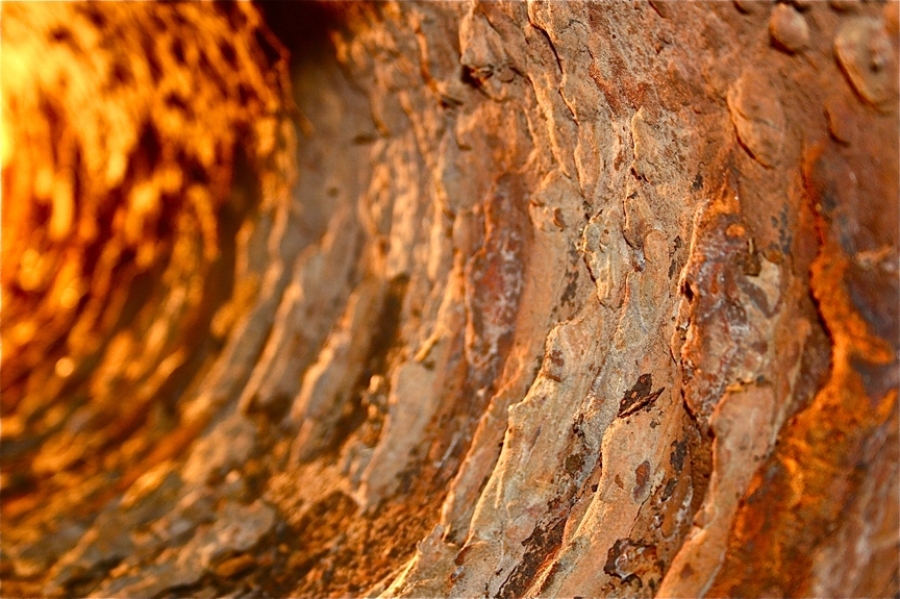
Para protegerlas, se han desarrollado diversos métodos y tecnologías que buscan prolongar su vida útil y garantizar su seguridad por lo tanto exploraremos los métodos de protección más comunes, la importancia de la preparación de la superficie para una protección efectiva y los estándares técnicos que los regulan.
MÉTODOS DE PROTECCION CONTRA LA CORROSIÓN.
Existen varios métodos para proteger contra la corrosión, que se utilizan según el tipo de material y las condiciones ambientales. Uno de los métodos más comunes es el uso de recubrimientos protectores, como pinturas o galvanizado, que crean una barrera física entre el metal y el ambiente corrosivo. Otro enfoque es el uso de inhibidores químicos, que se agregan al ambiente o al metal para reducir la velocidad de corrosión. Además, se pueden emplear métodos electroquímicos, como la protección catódica, que consiste en hacer que el metal a proteger se comporte como un cátodo en un circuito electroquímico, lo que evita la corrosión.
Pinturas Anticorrosivas.
Las pinturas son uno de los métodos más comunes de protección contra la oxidación. Estas pueden contener pigmentos inhibidores de corrosión que forman una barrera física entre el metal y el ambiente, evitando así el contacto directo con el oxígeno y la humedad. Además, las pinturas pueden contener aditivos ignífugos para mejorar la resistencia al fuego de la estructura.
Protección Catódica.
Este método se basa en la aplicación de corriente eléctrica para proteger el metal contra la oxidación. Se utiliza principalmente en estructuras enterradas o sumergidas, donde la corrosión es más probable. La protección catódica puede lograrse mediante ánodos de sacrificio o sistemas de corriente impresa.
Revestimientos de Fibras y Polímeros.
Los revestimientos de fibras y polímeros ofrecen una protección duradera contra la corrosión y el fuego. Estos materiales se adhieren a la superficie del metal y forman una capa protectora que evita el contacto directo con agentes corrosivos e ignífugos.
Galvanización en Caliente.
Este proceso consiste en sumergir la estructura metálica en zinc fundido para crear una capa protectora de zinc en la superficie del metal. La galvanización en caliente es altamente efectiva para proteger contra la oxidación, especialmente en ambientes agresivos.
Galvanización electrolítica.
El galvanizado electrolítico es un proceso utilizado para recubrir metales, como el hierro o el acero, con una capa delgada de zinc. Este proceso se lleva a cabo sumergiendo la pieza metálica en una solución de sales de zinc y aplicando una corriente eléctrica. El zinc se deposita sobre la superficie del metal mediante un proceso electroquímico, creando una capa protectora que ayuda a prevenir la corrosión.
NORMAS TÉCNICAS Y REGULACIONES RELATIVAS A LA CORROSIÓN.
Son fundamentales para garantizar la calidad y durabilidad de los productos y estructuras metálicas. Establecen los requisitos y procedimientos para la prevención, control y evaluación de la corrosión en diferentes industrias y aplicaciones.
Algunas de las normas más relevantes serian:
- ISO 12944: Esta norma establece los principios generales para la protección de estructuras metálicas mediante sistemas de pintura y revestimiento.
- ISO 9223: establece las clases de corrosividad atmosférica en función de la concentración de contaminantes.
- ASTM A123/A123M: Especificación estándar para galvanizado en caliente de productos de hierro y acero.
- NFPA 850: Código para la protección contra incendios de instalaciones industriales y comerciales.
- UL 1709: Norma para la evaluación de sistemas de protección contra incendios de estructuras metálicas.